Con una vasta gamma di prodotti – si parla di quasi un milione di referenze – indirizzati a molteplici comparti, Parker si configura come azienda di riferimento a livello mondiale nelle tecnologie di ‘Motion&Control’.
Nel settore delle life science offre soluzioni per la gestione, la purificazione e il controllo dei fluidi, nonché per la filtrazione, per la generazione di gas e per la gestione delle temperature, con applicazioni sia in ambito medicale, sia per i processi farmaceutici e biotecnologici. Di particolare interesse i sistemi automatizzati monouso integrati che accelerano i tempi di sviluppo, aumentano efficienza e sicurezza del processo e garantiscono la riproducibilità del prodotto. «Un tempo – spiega Enrico Cicolari – filtration & process key account manager di Parker Hannifin Italia – venivano impiegati sistemi fissi in acciaio e filtri riutilizzabili, ma filtrare consecutivamente più prodotti creava problemi di contaminazione, per il permanere di residui della lavorazione precedente. Inoltre occorreva sterilizzare tutto l’impianto accertandosi che il vapore arrivasse in tutti gli angoli delle linee. Bisognava eseguire vari processi di convalida per certificare che il vapore avesse sterilizzato tutta la linea di produzione e avesse rimosso le lavorazioni precedenti».
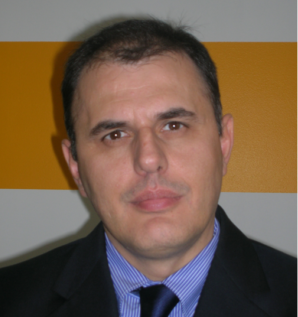
Come si sono evoluti questi sistemi?
Da queste linee fisse in acciaio si è passati all’utilizzo di single use system. Questi sistemi si adattano particolarmente alle produzioni biofarmaceutiche: specialmente per i “biofarmaci” ad alto valore aggiunto, per i quali una contaminazione sarebbe molto pericolosa e comporterebbe un enorme spreco di tempo e denaro, nel processo industriale si sta passando al dispositivo monouso.
Le aziende tendono ad acquistare un unico assemblato, spesso “customizzato”, come le sacche dotate di un filtro per liquidi e un filtro vent di sfiato avvolte in molteplici protezioni realizzate in polimeri speciali (Ldpe, Lldpe,Uldpe, Evoh). Tutto viene personalizzato su misura del cliente: il prodotto viene montato come fossero delle “catene da montare su uno pneumatico”, tutto il sistema viene pre-sterilizzato ai raggi gamma o è sterilizzabile in autoclave dal cliente; viene caricato e incanalato attraverso un filtro sterilizzante, dopodiché viene processato in base alla tipologia di prodotto e alle esigenze del cliente. La soluzione rappresenta un notevole risparmio di tempo perché, una volta assemblato da operatori nelle camere sterili, il sistema è controllato da vari sensori di pH, conducibilità, temperatura e pressioni, che comunicano con la pompa e ne regolano la portata arrestandola in caso di allarme.
Quali vantaggi presenta il monouso?
Il vantaggio principale è evitare la cross contamination. Tutti questi sistemi vengono identificati tramite codici a barre e se non c’è corrispondenza tra ricetta e assemblato la macchina non si avvia. L’automatismo vuole ridurre a zero il pericolo di contaminazione, perché ci sono variabili che possono influenzare il processo farmaceutico che vanno da un problema di materie prime, alle apparecchiature usate, a errori di misurazione, ma che comprendono soprattutto l’errore umano che in molti casi incide fortemente sui costi di produzione.
Avere una macchina in grado di annotare e pesare il prodotto, compensando in automatico eventuali variazioni di pH della soluzione tampone, e mantenendo traccia di ogni operazione (data logging), rappresenta un importante passo avanti per le aziende, un salto di qualità che aumenta la robustezza del sistema produttivo, con variabili ridotte al minimo.
In sintesi, disporre di sistemi integrati automatici di riempimento stand alone che utilizzano dispositivi monouso per la filtrazione e il dispensing farmaceutico in asepsi, significa poter lavorare con sistemi chiusi, integrati, automatici per il riempimento in condizioni asettiche, tramite preassemblati dedicati che, una volta svolto il loro compito, vengono rimossi e sono pronti per una nuova lavorazione. Non si ripresenta dunque più il problema di un prodotto a contatto con materiali non idonei.
Significa quindi, in sintesi, avere il processo sotto controllo, e la parola controllo è oggi uno dei comandamenti del mondo farmaceutico: non a caso Parker si definisce “il leader mondiale nelle tecnologie Motion&Control”.
Quali convalide devono passare i vostri dispositivi?
Dal singolo tappo, al tubo, al filtro, tutto deve essere rigorosamente studiato secondo i requisiti richiesti dalla Farmacopea americana e quella europea. Parker fornisce quindi tutti gli studi e i certificati necessari in accompagnamento al prodotto.
L’azienda è in grado di fornire bag dove le materie prime vengono stoccate anche per mesi e, a tal riguardo, produce studi di convalida per eventuali migrazioni o per la respirazione delle sacche, dato che possono essere permeabili al passaggio di gas, compresi l’ossigeno o l’azoto atmosferico. Il servizio comprende la valutazione dei tempi previsti dal cliente per lo stoccaggio e, per ogni periodo, la realizzazione dei necessari studi sulla cessione di sostanze tra il materiale della sacca e il prodotto farmaceutico.
Parker possiede propri laboratori chimico-farmaceutici dotati di tutti gli strumenti necessari per monitorare eventuali monomeri plastici presenti nel prodotto. Questi laboratori sono principalmente localizzati in Inghilterra e in America. Non occorre siano presenti in tutti i Paesi in cui opera l’azienda, dato che è possibile trasferire la merce talmente rapidamente che lo studio può essere effettuato anche dall’altra parte del mondo e fornire i risultati dell’analisi quasi immediatamente. L’importante, semmai, è che questi laboratori siano molto attrezzati e avanzati tecnologicamente.