Fondata settant’anni fa, era infatti il 1947, con la denominazione Industria Nazionale Guarnizioni Ermetiche, fil rouge della crescita di INGE sono i materiali plastici, che hanno vissuto un’irresistibile ascesa sino ad affermarsi come insostituibili strumenti della vita quotidiana.
[metaslider id=23517]
Alla fine degli anni Sessanta, l’azienda specializza la sua produzione rivolgendosi al packaging primario farmaceutico, settore che rappresenta ancora oggi il core business della società che, nel frattempo, ha iniziato a operare anche in ambito nutrizionale, cosmetico, veterinario e della diagnostica.
Entrato in azienda nel 1993, il dottor Alessio Nobbio – laureato all’università Bocconi e con un master in MBA – dal 1996 è alla guida di INGE SpA: NCF l’ha incontrato.
INGE è un referente di primo piano nella produzione di packaging primario in plastica: quali sono i vostri punti di forza?
In questi settant’anni di attività abbiamo costantemente sviluppato, qualitativamente e quantitativamente, le nostre potenzialità tecniche e produttive, grazie anche alla dedizione e passione dei nostri dipendenti, uomini e donne che hanno reso possibile il raggiungimento di importanti traguardi.
Struttura e organizzazione si distinguono da quelle dei nostri competitor, perché sono state costantemente pensate per rispondere alle richieste del mercato attraverso una partnership a 360°; siamo pertanto in grado di seguire tutte le fasi, dallo sviluppo alla produzione, contando al nostro interno, ieri come oggi, su un ufficio tecnico che progetta le soluzioni, un’officina meccanica che realizza, a partire dall’acciaio, le attrezzature e gli stampi necessari, la produzione.
Quest’attitudine self made rappresenta un significativo valore aggiunto: i nostri partner possono avere come interlocutore un unico soggetto che si occupa di gestire il complesso iter progettuale del prodotto e, qualora necessario, rispondere alle loro necessità anche in tempi strettissimi, richiesta difficilmente rispettabile se dovessimo appoggiarci a studi e officine esterni.
È importante, inoltre, sottolineare che abbiamo alcune linee standard, ma la gran parte del materiale che produciamo è su commessa, ed è stato studiato e personalizzato in base alle esigenze del singolo cliente. Un ulteriore servizio a disposizione dei nostri partner è la possibilità di usufruire del nostro magazzino di 5000 m2 – che si trova a Garbagnate Milanese, dove abbiamo ormai cinque siti per un totale di 15.000 m2 – dove potranno lasciare in deposito il materiale fino al momento della loro produzione.
I brevetti che avete sviluppato sono centinaia…
280 per la precisione… e purtroppo talvolta ci è capitato di vederne alcuni presentati sul mercato da altre aziende che se ne assumevano la paternità.
Si tratta di un numero che dimostra ancora una volta quanto l’orientamento di INGE sia, da sempre, fortemente rivolto al continuo miglioramento dei prodotti e allo studio di nuove soluzioni, tecnologie e materiali. Sfogliando i tantissimi progetti brevettati, troviamo anche oggetti di uso comune, a partire dai tappi di plastica con il collarino per le bottiglie di vetro ai tacchetti per le scarpe da calcio, alle giarrettiere per le calze da donna, solo per fare alcuni esempi. Nel 1965 abbiamo studiato, brevettato e industrializzato il primo tappo separatore di sostanze liquido-polvere per un’importante azienda farmaceutica italiana.
La realtà odierna del mondo industriale è indubbiamente più complessa rispetto a quella del dopoguerra, ma l’attività di ricerca e sviluppo continua a essere centrale nel nostro modello di fare impresa.
Tra le innovazioni più recenti, per esempio, troviamo il tappo separatore per ingredienti attivi Long Life Cap™ (vedi box) o il modello Push and Mix Cap™ che trova molteplici applicazioni: integratori alimentari, multivitaminici, fragranze per acqua, latte in polvere, bevande per bambini, sport drink, soluzioni estemporanee in acqua per animali. La sua versatilità lo rende un tappo speciale, realizzato in diverse versioni e capacità per poter formulare soluzioni sia in polvere che liquide.
Un altro vantaggio esclusivo è la sua bocca; infatti, è possibile applicarlo a tutte le bottiglie di acqua e per soluzioni farmaceutiche e nutraceutiche e a tutti i flaconi con capacità diverse e bocche standard. Il suo uso è estremamente intuitivo: con un semplice gesto si preme la parte superiore e questo permette di forare la pellicola e liberare il contenuto del tappo che verrà miscelato alla soluzione liquida.
Oltre alla semplicità di utilizzo, sono soluzioni che rispondono a un modello di produzione più ecosostenibile…
Abbiamo “semplificato” il packaging primario, dimezzando in taluni casi la quantità di PE necessaria per la sua produzione, e riducendo contestualmente il consumo di energia e la quantità di materiale da smaltire una volta utilizzato, il tutto in una prospettiva di produzione ecosostenibile che inevitabilmente si farà più pressante nei prossimi anni.
Sempre in questa prospettiva abbiamo introdotto l’utilizzo, per alcune produzioni, di Ingeo PLA, un innovativo biopolimero della statunitense NatureWorks prodotto attraverso una tecnologia brevettata di polimerizzazione dell‘acido lattico derivante dalla fermentazione degli zuccheri di piante come il mais e le barbabietole. Si presenta come un materiale assolutamente trasparente di grande brillantezza e chiarezza, facilmente formabile e stampabile, e può essere lavorato come una qualsiasi plastica tradizionale. Oltre a essere prodotto da fonti annualmente rinnovabili – con l’uso del 50% in meno di energia non rinnovabile rispetto ai polimeri tradizionali come il PET o il polistirene e con la produzione del 60% in meno di gas a effetto serra – il biopolimero PLA, o acido polilattico, è biocompostabile secondo la norma EU 13432 che prevede la totale decomposizione del materiale in un tempo corrispondente a quello necessario per la decomposizione della carta e senza la produzione di alcuna sostanza tossica.
Avete una produzione annua rilevante: quali le percentuali di mercato? Per quanto riguarda l’estero, in quali paesi siete presenti?
I pezzi venduti all’anno sono più di 450 milioni, il 55% destinato al segmento pharma, a cui segue il mercato nutrizionale (25%) e il restante 25% suddiviso tra gli altri settori. Le esportazioni hanno raggiunto il 40% della produzione; il principale mercato di riferimento rimane l’Europa, ma siamo presenti anche negli Stati Uniti, in America Latina in alcuni paesi asiatici.
Il know-how che abbiamo maturato e consolidato nella nostra lunga storia ci permette di fornire la risposta giusta anche in ambiti tecnicamente molto avanzati. In campo diagnostico, per esempio, ci vengono richiesti contenitori per esami di laboratorio triangolari o cilindrici che devono adattarsi alla strumentazione; un altro innovativo progetto al quale abbiamo collaborato ha riguardato la ricerca di uno speciale contenitore per eseguire l’analisi immediata del sangue, da utilizzare quindi in situazioni di emergenza e sulle ambulanze, che doveva essere funzionale per la lettura, attraverso un software, dagli strumenti mobile.
Il tappo “tutto in uno”
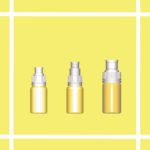
Long Life è un tappo separatore per ingredienti attivi – per esempio i probiotici e i multivitaminici che sono inclini alla biodegradazione – ed è costituito da un unico componente che applicato su un flacone monodose costituisce un’efficace barriera tra miscela solida e soluzione. Da numerosi studi comparativi di stabilità, come test di controllo e misurazione dell’umidità relativa, è risultato che, grazie alla loro bassissima permeabilità al vapore acqueo, i tappi separatori Long Life sono in grado di assicurare una più elevata protezione nei confronti dell’umidità garantendo l’ottimale shelf-life del prodotto. Si tratta di un packaging facile da utilizzare, perché è sufficiente premere l’estremità superiore del tappo per rilasciare il contenuto attivo e, successivamente, agitare e svitare per rimuovere il tappo dal flacone rompendo il sigillo di garanzia. La capacità di contenimento della linea dei tappi separatori Long Life è di 0,5, 1 e 1,5 ml ed è applicabile a flaconi in PE, PET e PLA con capacità di 10, 15 e 20 ml.
INGE, certificata Uni e Iso 9001:2008, produce dal 1947 sistemi di packaging primario in materiali plastici per l’industria farmaceutica, cosmetica, diagnostica e nutraceutica. Nella sede di Garbagnate Milanese, dove lavorano circa 90 dipendenti, l’azienda dispone di una divisione R&D per lo studio di nuovi prodotti anche personalizzati; in tre distinti reparti (stampaggio a iniezione, iniezione-soffiaggio e iniezione-stiro-soffiaggio, estrusione-soffiaggio) sono attive più di 50 linee di produzione, di cui molte in ambiente a contaminazione controllata classe 100.000. Inoltre, sempre internamente, l‘azienda è attrezzata per progettare e produrre gli stampi, per decorare e serigrafare fino a cinque colori i prodotti, assemblarne i componenti e confezionarli in blister e flowpack. Nel 2016 è stato inserito il primo robot che lavora in autonomia su un’imbustatrice. Complessivamente, sono più di 2000 gli stampi realizzati per particolari e per flaconi in resina termoplastica (PE, PP, PET, PETG, PS ecc.). Le linee dell’azienda comprendono: flaconi per uso diagnostico; misurini e cucchiaini per sciroppi; microclismi e macroclismi; monodose e separatori di sostanze; prodotti ginecologici; packaging oftalmico e per naso, orecchie e gola; flaconi per talco; pilloliere; flaconi per insetto-repellenti.